The electric vehicle (EV) revolution, once hailed as an unstoppable force, is encountering a significant hurdle: the burgeoning used EV market. While new EV sales continue to climb, albeit with some recent fluctuations, the secondary market is proving to be a complex and, for some, a concerning landscape.
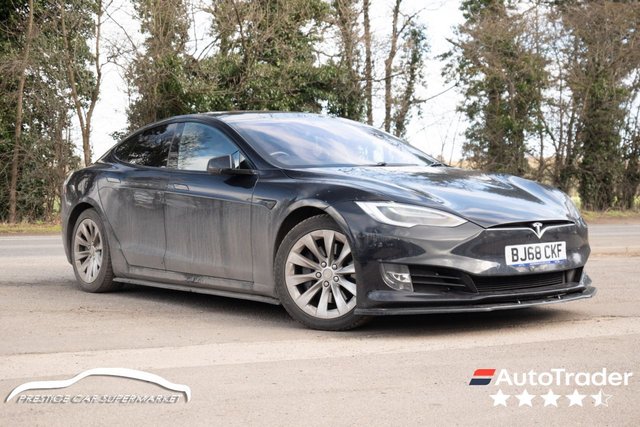
Why the Used EV Market Matters:
A healthy used EV market is crucial for wider EV adoption. It provides a more affordable entry point for consumers hesitant to commit to a brand-new vehicle. It also ensures that the environmental benefits of EVs are maximised, extending their lifespan and reducing the need for new car production. However, several factors are currently creating challenges.
The Challenges:
- Rapid Technological Advancements and Battery Degradation Concerns:
- EV technology, particularly battery technology, is evolving at a breakneck pace. Newer models boast longer ranges, faster charging, and improved software, making older models feel quickly outdated.
- Concerns about battery degradation, while often overblown, still linger in the minds of potential buyers. Uncertainty about the long-term health and performance of used EV batteries is a significant deterrent.
- The lack of standardised battery health assessments across manufacturers adds to the confusion.
- Depreciation and Pricing Volatility:
- EVs, especially early models, have experienced rapid depreciation. This can be attributed to the factors mentioned above, as well as fluctuating new EV prices and government incentives.
- This depreciation makes it difficult to accurately price used EVs, leading to price volatility and uncertainty for both buyers and sellers.
- Charging Infrastructure and Range Anxiety:
- While charging infrastructure is improving, it’s still not as widespread or reliable as traditional gas stations. This can deter potential buyers, especially those living in areas with limited charging options.
- Range anxiety, the fear of running out of battery charge, remains a concern, particularly for those considering older EVs with shorter ranges.
- Software and Over-the-Air Updates:
- Newer cars have better software, and often recieve over the air updates. Older cars may lack these updates, and therefore lack newer features. This makes older cars less desirable.
- Supply and Demand Imbalances:
- The market is still adjusting to the increased supply of used EVs as leases expire and early adopters upgrade. This, combined with fluctuating demand, creates price instability.
What’s Being Done?
- Manufacturers and third-party companies are developing battery health assessment tools to provide greater transparency and confidence to buyers.
- Efforts are underway to expand and improve charging infrastructure, addressing range anxiety.
- Increased transparency from manufacturers regarding battery warranties and expected lifespans is needed.
- More standardised software updates would help keep older cars more relevant.
The Road Ahead:
The used EV market is still in its early stages. As technology matures, infrastructure improves, and consumer confidence grows, the market is expected to stabilise. However, addressing the current challenges is crucial for ensuring the long-term success of the EV revolution.
The used EV market is a critical piece of the puzzle, and its evolution will play a significant role in shaping the future of transportation.