Ammo NYC founder Larry Kosilla brings an obsessive attention to detail to everything he does, including the space where he works on cars. After outgrowing his home garage, Kosilla set out to build the ultimate detailing garage, a process that took about a year.
Kosilla started with an existing building, working with an architect on an extensive remodeling. The building is divided into three areas, including garage bays on the ground level, an office, and an editing suite for videos shot in the garage.
To convert the ground level from its previous function as an art studio to a garage, core samples were taken to ensure the concrete could support heavy vehicle lifts. The lift locations were then mocked up with cardboard, and cuts were made in the appropriate places. Pipes were also installed in the floor for the lifts’ hydraulics, and in the walls for a central vacuuming system that can be used for cars in the garage bays, or to clean upstairs spaces.
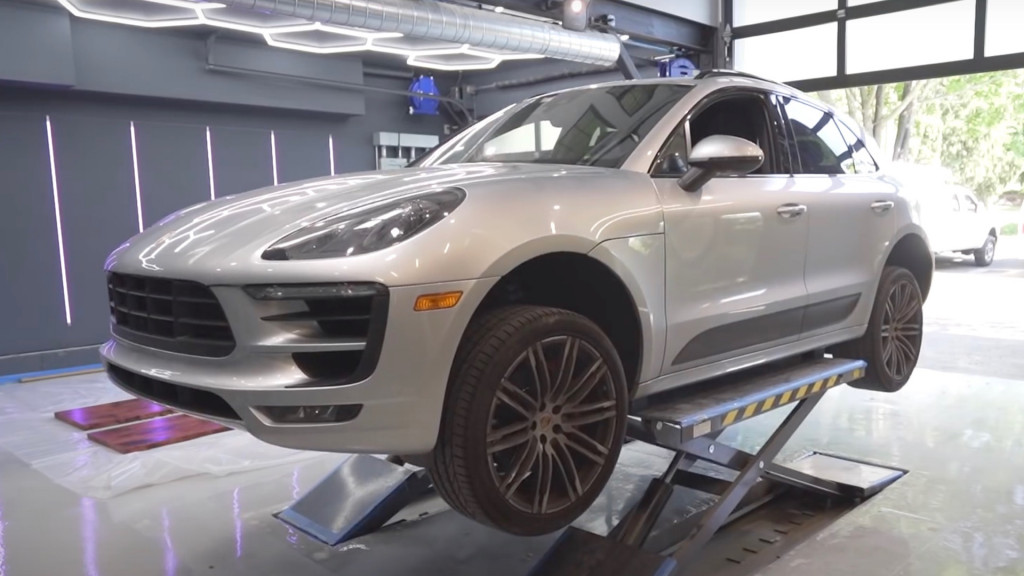
Ammo NYC detailing garage
Kosilla also outfitted the garage with custom-built Moduline cabinets and Prevost air lines, the latter featuring a snazzy blue enamel coating.
The garage floor got an epoxy coating with a UV protectant and an additional layer to “knock down” the gloss finish, as powerful lights were also installed in the garage bays that could damage the finish, or produce excess glare that would be picked up by camera lenses. Walls, meanwhile, were painted gray to keep the focus on the cars.
Watch the full video for complete details on this build. It’s part car video, part home-improvement how-to.